成都领克——数字化转型时代先锋
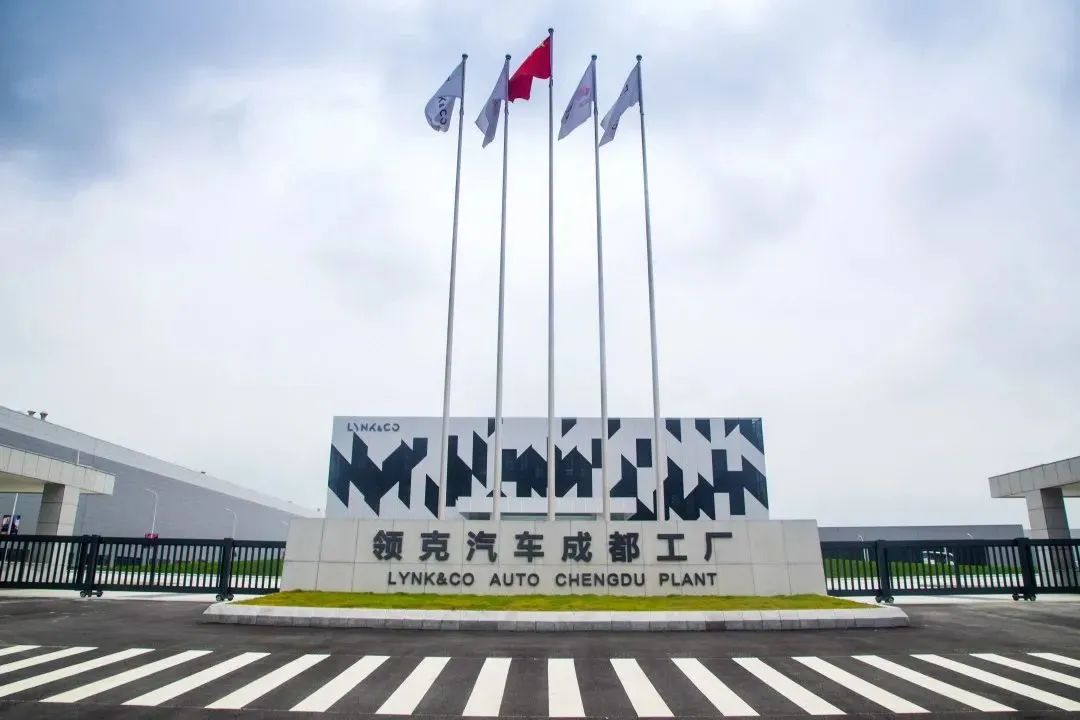
LYNK&CO
什么是“无人工厂”?
629 — 它有629台机器人;
317 — 它有317台 AGV小车;
940 — 它有940台自动化设备;
385 — 它有385台工位和自动化设备终端联网;
3500 — 它有3500个关键质量点均进行信息采集管理,可大数据记录分析,实现 “一车一档”。
其实准确来说它应该叫作“高度智能化和全面信息管理工厂”。
“十四五”规划指出,加快推动社会数字化进程,让数字资产和实体产业深度融合,赋能“数字中国”发展。行业内围绕数字化转型和智能制造2025摩拳擦掌。
在此数字化转型升级的浪潮中,企业如何抓住新一轮工业变革红利,开启企业发展新通道?这是需要企业间广泛交流、共同探索的时代命题。
想要交上满意的答卷,势必要突破企业沟通交流屏障,开启同创共赢、相融共生的发展新篇章。
成都领克汽车有限公司(以下简称“成都领克”)工厂在数字化转型方面做了许多尝试,如利用算法进行冲压的自动排产,降低了冲压件的库存,提高了排产的工作效率及准确度,同时车间内的所有物料、工装器具的状态在系统内信息透明;开发了模具管理系统,并与MES 及设备系统联通,使得模具状态信息、检修工单、各类报表等可以及时高效地传递,降低了模具故障率。还有其他压机状态监测等。
成都领克获得工信部授予的互联网应用试点示范、数字化转型领航企业等3 项国家荣誉称号。小编将带领各位读者一起走进成都领克的数字化工厂,为大家展示智造与创新的完美结合。
智能工厂,科技感的“源泉”
据工作人员介绍,领克汽车成都工厂是全球最具先进性的汽车生产基地之一,是严格按照世界级工厂标准建设而成。工厂规划之初就以“工业4.0理念”为蓝本,引入了完善的IT系统、先进的信息管理模式、一流的高精尖设备、全球统一的严苛豪华品牌制造标准等,实现了高度智能化、无人化、定制化、柔性化生产。
更值得一提的是,领克汽车成都工厂又被称为“无人工厂”!
全厂配备了629台机器人,317台AGV小车,具有高度自动化,可实现高效低耗生产。
在整车的生产过程中,工厂内940台自动化设备及385台工位进行终端联网,3500个关键质量点均进行信息采集管理,通过大数据记录分析,完美实现一车一档质量信息精准追溯。
制造离不开创新,制造更要“智造”。
视觉+AI自动收货,自动分拣,无人配送……在领克汽车成都工厂总装车间,工人只需在固定位置进行操作,其余零配件都由各种“机器”配送到跟前。
“工厂内配备了行业领先的智能工位终端,引导物流生产流程,大幅度提高物流运行效率。加之,底盘整体合装技术和关键力矩信息化控制技术的植入,最大限度地保证了产品质量。”领克汽车成都工厂相关负责人说。
可以说,领克汽车成都工厂拥有世界顶级的智能化生产工艺及信息管理技术。
数字化转型初期如何攻坚克难?
对一家传统制造企业而言,进行数字化转型面临着一系列的难点需要突破,成都领克生产物流部工艺总工程师/数字化总监颜正钊以成都领克建立数字化工厂的过程中为例,以行业痛点为抓手,介绍了企业在数字化转型初期攻坚克难的具体内容。
首先,数据采集和清理。
数字化转型工作的基础就是数据,需要一个数据平台(IoT),各类数据可以通过工厂大脑(数据驾驶舱)的方式,给经营层起到决策辅助的作用。
其次,消除各个信息系统的孤岛。
传统制造行业大量运用MES、LES、ANDON 等各类系统,各个系统形成孤岛,效率非常低下。如何联通这些信息化的系统,联通后系统间数据如何共享并给业务高效赋能是关键。
再次,专业应用系统缺失。
我国制造业经历二十多年的快速发展,现已经形成一套完整的目视化管理以及纸质化的分析、存档、追溯流程,在智能制造转型过程中则需要借助信息化及数字化的手段,来替代上述传统管理和问题处理分析工具,而针对传统制造业专门开发的适配各个专业的定制化系统,目前在国内还是非常少见的。
最后,人员意识变化和技能培养。
传统制造行业的从业人员缺少互联网的思维以及系统开发流程经验,不知道哪些行业痛点可以通过数字化的手段解决,而互联网的从业人员又不懂制造行业的专业流程,无法找到切入点给制造赋能。这就需要培养一批解决方案专家,应用数字化方式解决业务痛点。
数字化转型洪流涌动,
各行各业加快转型变革。
随着数字化转型日趋深入,
行业知识与专业技术的耦合就愈发深入,
唯有行业伙伴、上下游协同企业相融共生,
方能真正实现创新变革、同创共赢,
在共同成长中共赢未来!

某省工业和信息化厅“英才名匠”走进阿里巴巴
50位“英才名匠”优秀领军企业家到杭州万事利集团、吉利汽车集团、阿里巴巴集团、华立集团、娃哈哈集团、梦想小镇研修 !企业家参访标杆、学习标杆、超越标杆,先僵化、再优化,最后再固化。阿里巴巴集团是全球数字经济的标杆企业,积累了大量丰富的数字经济时代发展经验。目前已经发展为电子商务、互联网金融、云计算大数据、智能物流骨干网、健康文娱、跨境贸易、人工智能等一系列业务的全球化高科技公司。学习阿里巴巴企业文化、管理三板斧和数字化,走进阿里巴巴游学。
参观比亚迪
比亚迪凭借硬核的作风和对技术执迷的追求,硬是从电池、汽车两个原本互不相干的领域杀出了一条血路,并且比亚迪超上汽,已经成为中国市值最大车企!企业家亲临比亚迪、参访标杆企业、学习标杆企业,不断对标,持续发现问题并解决问题,对标一流企业经营管理实战经验,与一流道场中的专家对话,与同行者切磋,碰撞观点,在纷繁复杂的变化中突破经验的限制,用独特视角洞见商业本质,把握方向和格局,建立适应未来的新系统,实现增长。比亚迪凭借独特的垂直整合模式,成功打造了具有国际水平的技术创新平台,在IT、汽车等多个领域不断推出领先世界的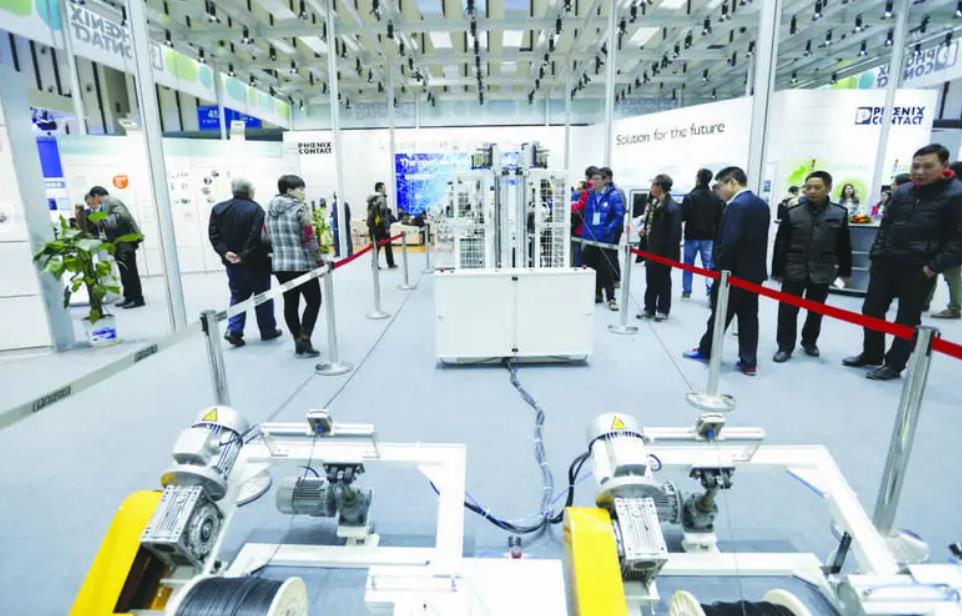
走进菲尼克斯
德国菲尼克斯电气集团已有八十多年的历史了,目前在全球近四十个国家拥有子公司,五十多个国家设有代表处。菲尼克斯电气中国公司自1993 年扎根南京,坚定与中国产业共同发展,成为德国集团海外最大的研发和生产基地、集团三大竞争力中心之一。企业家参访标杆、学习标杆、超越标杆,先僵化、再优化,最后再固化。企业家亲临标杆,寻找与一流企业差距,建立追求卓越的思维模式;不断对标,持续发现问题并解决问题;发现和一流企业经营管理实践背后的结构,有所创新与突破。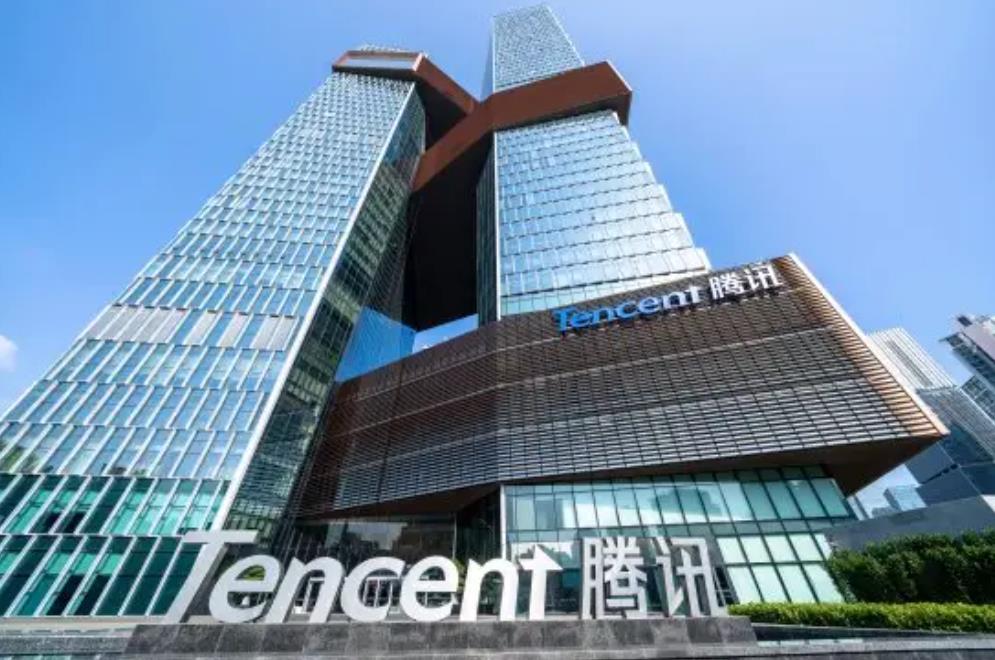
学习腾讯
企业家游学腾讯,参访标杆企业,标杆学习最好的方式是先僵化,再优化,最后再固化。腾讯是中国最大的互联网综合服务提供商之一,也是中国服务用户最多的互联网企业之一。考察研学腾讯,学习腾讯的组织、文化和数字化创新,企业家学习标杆企业就是要走进标杆,学习原汁原味的标杆。企业家访学腾讯,提高认知和拓展视野,选择专业机构三体文明游学。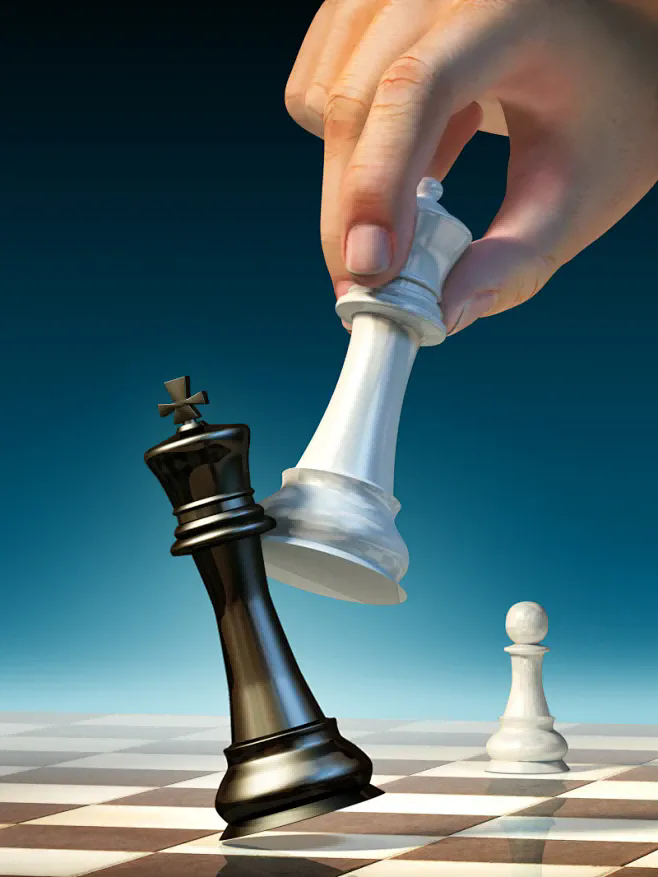
逃离“百度式”平庸:用终局思维打造不可替代的战略优势
终局战略为企业在不确定时代提供了关键指引,通过精准判断未来市场趋势,助力企业提前布局、优化资源配置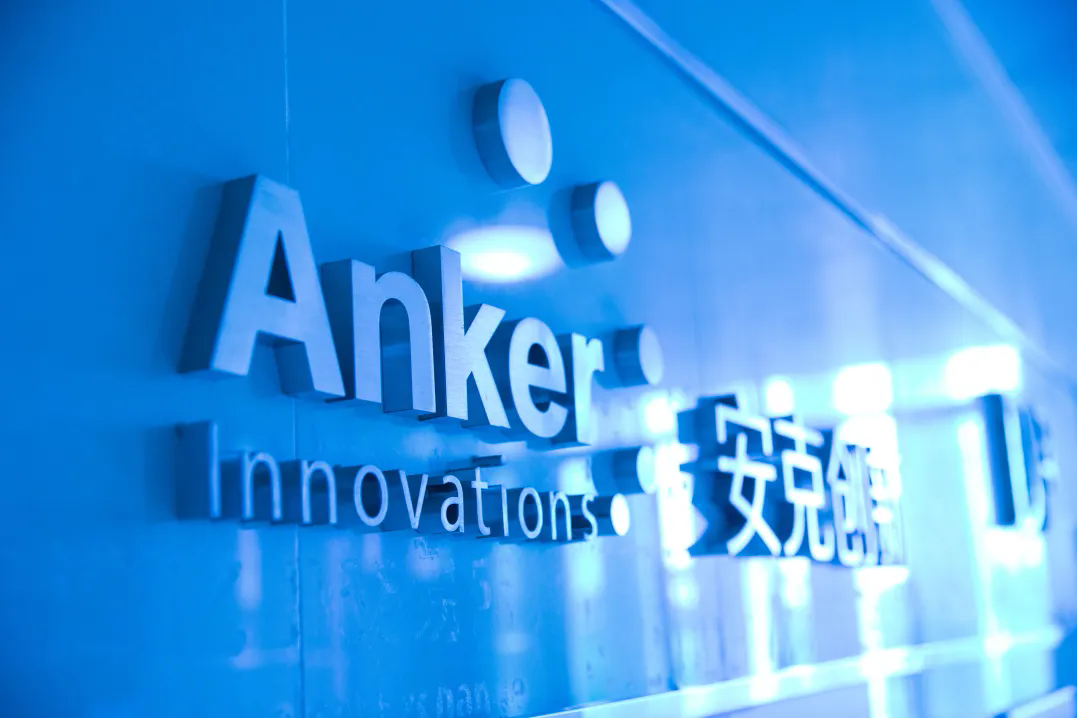
从0到15亿:安克创新如何用“本土化”策略打开全球市场?
在许多企业为创新方向发愁时,安克创新的成绩令人羡慕。但我们不禁想问:它是如何做到的?一家跨境电商企业,是如何成功打造自有品牌的?在发展过程中,它克服了哪些挑战?未来又将走向何方?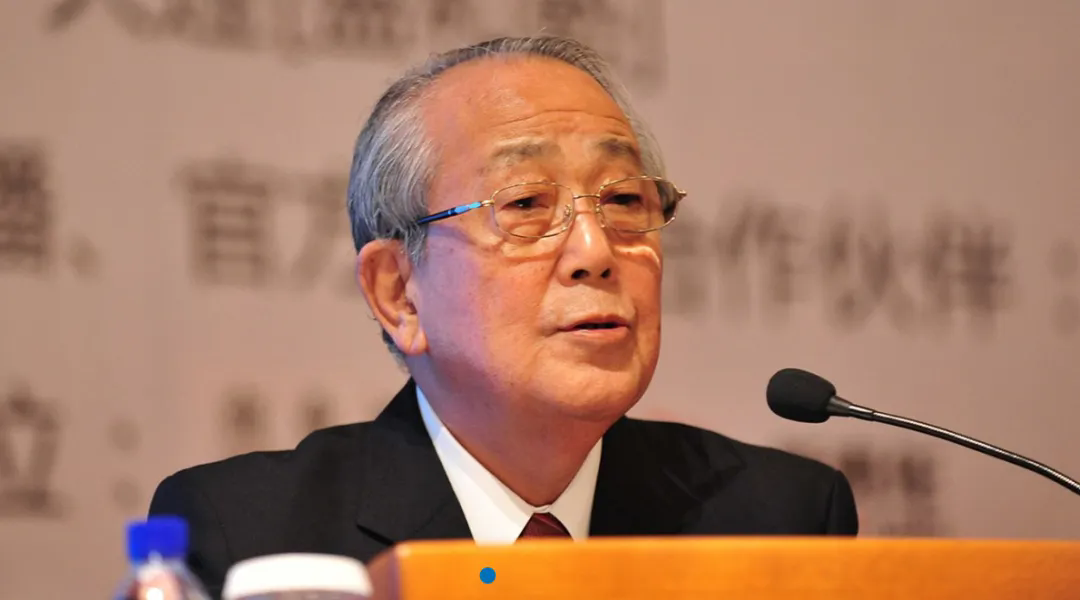
稻盛和夫:越难的事,越要做
标杆企业、标杆企业参访、游学、稻盛和夫、智能制造、标杆学习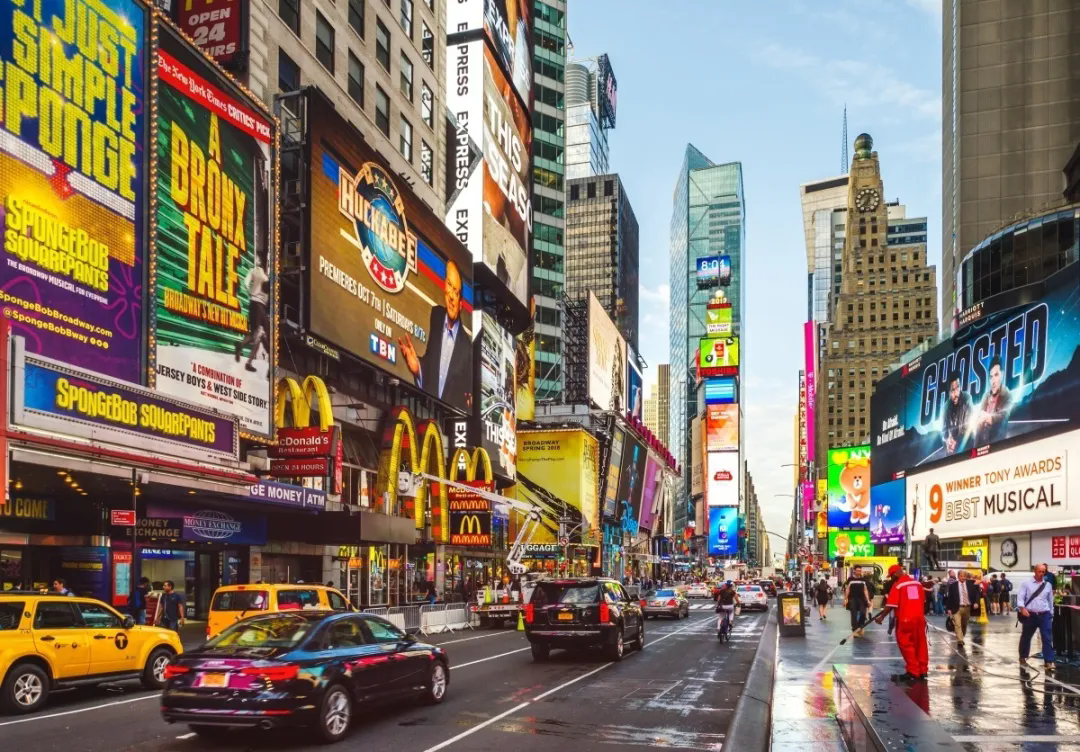